NEWS
High quality placement using inline soldering
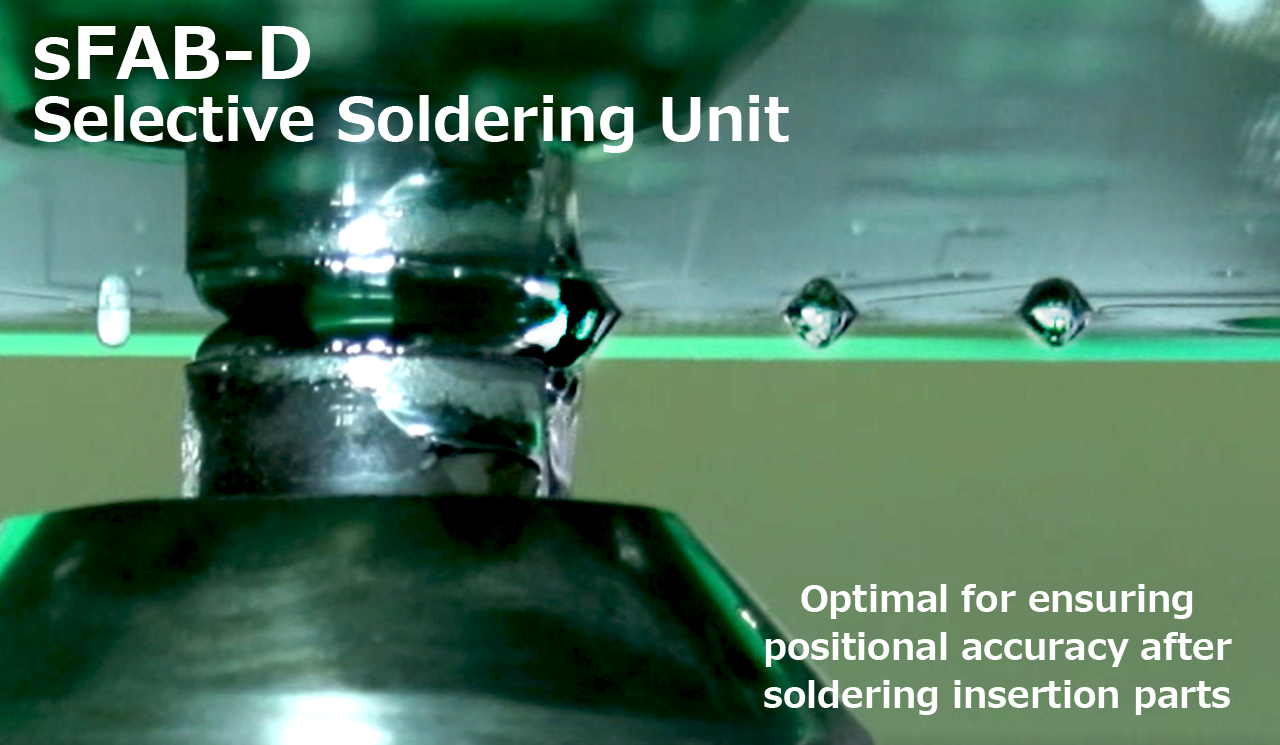
There are insertion parts that require control of the insertion stance and height, and these kinds of parts require stabilizing jigs and spacers to be able to solder using wave soldering. However, such a method increases the amount of work and requires there to be dedicated jigs and pallets for each panel, which increases the amount of management work as well as increasing the cost.
Multipurpose Automated Fabrication Machine – sFAB-D together with the selective soldering unit is an effective solution for this kind of production.
Features and advantages
- The part is held in position after insertion while the solder is being applied so that parts do not shift or fall over, and can also be secured at the required position and height.
- The appropriate amount of solder is applied because the soldering time can be set individually for each part. This prevents issues such as insufficient solder or solder bridging.
- Because the fountain nozzle can be moved to the exact spots that require soldering, no mask pallets are required for protecting parts that should not be soldered.
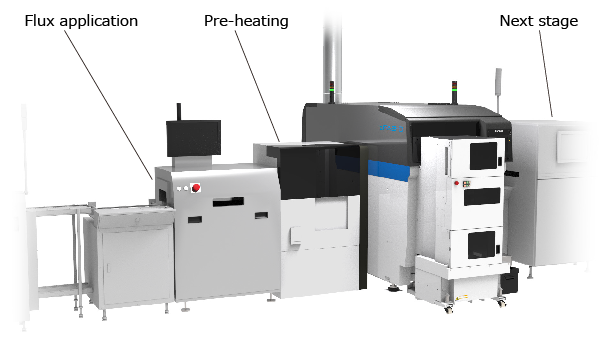
Applications
Managing the part height
When wave soldering parts that need the height to be controlled, it is necessary to use a spacer between the part and the panel. The sFAB-D holds the part in place while using selective soldering, so that soldering can be performed at a consistent height without manual intervention.
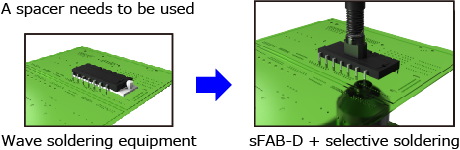
Highly accurate positioning of set parts
The connector pitch needs to be aligned correctly both above and below for connectors that connect two panels together. By soldering with the part being held in position, parts can be secured with high positioning accuracy without using positioning jigs.
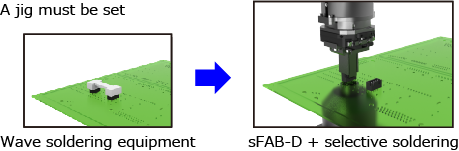
Soldering with the optimal conditions for each part
Because the selective soldering uint applies the appropriate amount of solder for each part, the rate of defects after soldering is dramatically reduced. Also, because there is no attachment or removal of mask pallets, something that would generally be used during the soldering process, there is less work involved.
Selective Soldering Unit specifications
Applicable boards |
Panel sizes |
50 x 50 mm to 400 x 324 mm |
---|---|---|
Panel thickness |
0.4 to 2 mm | |
Premounted part height on the other side |
25.4 mm | |
Dead space during fountain nozzle operations |
15 mm from edge of the panel to the center of the fountain nozzle |
|
Dead space in the conveyor clamping area |
3 mm from panel edge |
|
Soldering application | Can select from: Insert parts first, insert & solder together, and solder trace | |
Soldering equipment | Solder pot capacity | 8 kg |
Solder tank temperature | Room temperature to 300 degrees C | |
Tact time | Depends on the soldering time | |
Pre-heater | Model | Infrared panel heater |
Exhaust | Heat exhaust | Heat exhausted from the factory exhaust system (Note 1) |
Flux fumes | Collected by a fume recovery head (note 2), or an extractor fan attached to the soldering unit. |
Note 1: This unit cannot be loaded to Side 2 because it has a dedicated cover
Note 2: Attached to the R head