NEWS
2021年度の実装技術動向と最新SMTソリューションの提案
1. はじめに
新型コロナウイルス感染症(COVID-19)の全世界へのまん延は、政治・経済・社会活動に大きな影響を及ぼし、生活様式の変容が急速に迫られた。ウィズコロナ時代において、在宅によるテレワークやオンラインツールを利用したミーティングも急速に浸透し、働き方が大きく変わった。これまでは業務の効率化や少子高齢化による労働人口不足を補うことを期待されたロボットも、様々な産業分野で感染リスクを低減させるために「遠隔化」、「非接触化」、「非対面化」を実現するサービスロボットとして活躍範囲を広げ、新たな価値が見出されている。また、感染拡大の抑制と警鐘を促すために、通信端末の位置情報を基にした人流データなどもニュースで良く耳にするようになったのではないだろうか。今後フィールドに散在するデータをソフト・ハードの両面で如何に活用するかが重要であることはいうまでもない。
我々が考えるポストコロナの未来社会「ヒト・モノ・データ・プロセスがつながる時代」を示す(図1)。 「ヒト・モノ・データ・プロセスがつながる時代」は衣食住・健康状態・購買・移動などの行動に関わる情報、気候や交通などの環境に関わる情報、企業の事業や業務に関わる情報など把握が困難であった情報がデジタル化され、ネットワークに繋がることで一元管理され、新しい価値が創出される。我々の取り組みは社会全体の一部だが、本稿では2021年度実装技術動向を述べたのち、我々のデジタルツインソリューションついての取り組みを紹介する。
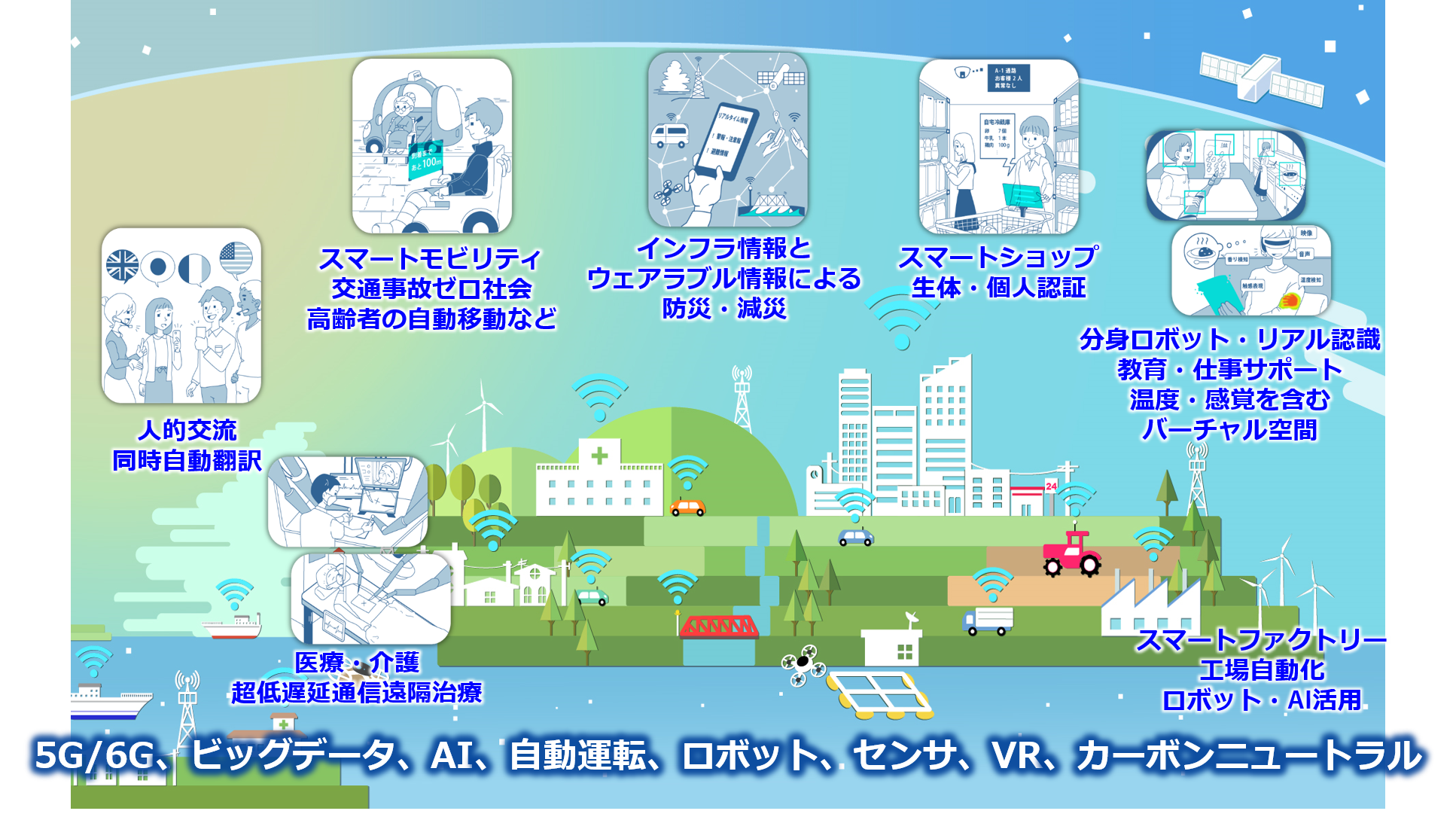
図1 未来社会 ヒト・モノ・データ・プロセスがつながる時代
2. 2021年度実装技術動向
2.1 SMT部品のトレンド
スマートフォンやスマートウォッチなどの通信端末の多機能化・高性能化、5GやIoEの普及によるネットワークインフラ、センサー機器の拡大、及び電気自動車の普及により、実装点数の増加は継続している。本章ではSMT部品のサイズ動向と半導体パッケージの動向を示す。
2019年度実装技術ロードマップ(JEITA 電子技術産業協会)によると積層セラミックコンデンサの構成比率は2018年度に0603Mと1005Mのクロスポイントを迎え、0603Mの構成比率が最も高い。スマートフォンは高機能化やバッテリーの領域を確保するために、実装エリアの縮小化や三次元化の要求がある。そのため今後も0402Mの構成比率が伸長し、2025年には20%程度になると見込む。0201Mも2022年にかけて普及が進むと予想する。また、受動部品の小型化以外にも隣接部品との隙間も年々狭くなってきており、2024年に50ミクロン前後になるとも予想される。部品間の隙間が狭い基板へ部品を装着する場合、吸着ノズルの先端が部品からはみ出すと、装着済みの隣接部品にノズル先端が干渉し、不良が発生するケースがある。このような場合、最適なノズル設計とノズルの選択が重要となる。今後、実装品質はより厳しい管理が必要になってくるが、顧客が安心して実装して頂けるよう、品質を担保した上で、高速化・高精度化を両立した実装機の開発を引き続き進める。
次に半導体パッケージの動向を示す。半導体パッケージは多ピン化の要求に伴う狭ピッチ化と薄型化が進み、大型QFP(Quad Flat Package)からBGA(Ball Grid Array)へ、小型QFPからQFN(Quad Flat Non-leaded)、WLP(Wafer Level Package)へシフトが進む。一方でサーバー製品向けは大型且つ高重量のBGA実装要求があり、現在モジュール型高速多機能装着機NXTでは標準仕様で102mm,特殊仕様で150mmまでのサイズに対応している。機器の高性能化に伴う多ピン化の傾向は共通であるが、アプリケーションによりサイズ・重量の特徴は異なる。
2.2 半導体パッケージングの実装ソリューション
SiP(System in Package)/モジュール製品の製造プロセスで共通しているのは、高密度化・薄型化・多層化などの最先端の実装技術が複合している点である。SiP/モジュール部品製造に対するFUJIのソリューションの抜粋を図2に示す。また、下図以外にも、基板自体が薄くなる中で実装品質を安定化するためには、薄厚基板のたわみを矯正し、部品装着面を一定の高さで保持しなければならない。そのため薄厚基板の保持にはバキュームバックアップが有効である。バキュームバックアップにより薄厚基板はバキュームプレート上面で吸着固定され、部品装着面を一定の高さで保持し、部品装着時の荷重による基板振動や基板反りの影響を最小化することができるようになる。
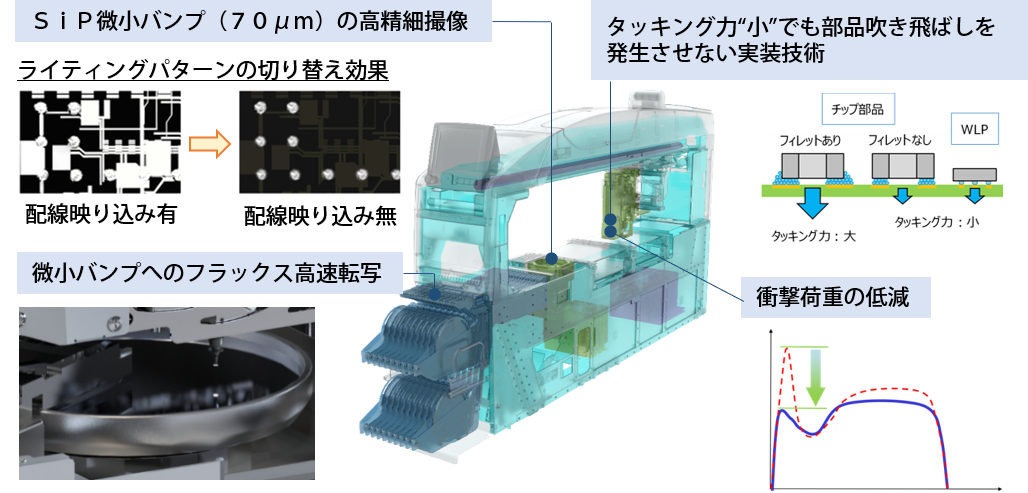
図2 SiP/モジュール製品生産に対するFUJIのソリューション
3. デジタルツインで進化するスマートファクトリー
3.1 SMTラインのデジタル連携
デジタルツイン技術を使ったスマートファクトリーを実現するために、SMTラインの更なる自動化とデジタル化を進めている。デジタルツインとは、仮想世界に現実世界の環境を構築し、仮想空間の中でシミュレーションを行い、現実世界で起こりうることを事前に予測し、制御することである。我々は電子部品実装機NXTR(図3)を中心としてAGVなどの周辺機器を稼働させるケースを想定し、デジタルツイン技術を活用した提案を行っている。本章は仮想世界・現実世界の我々の取り組みを紹介する。
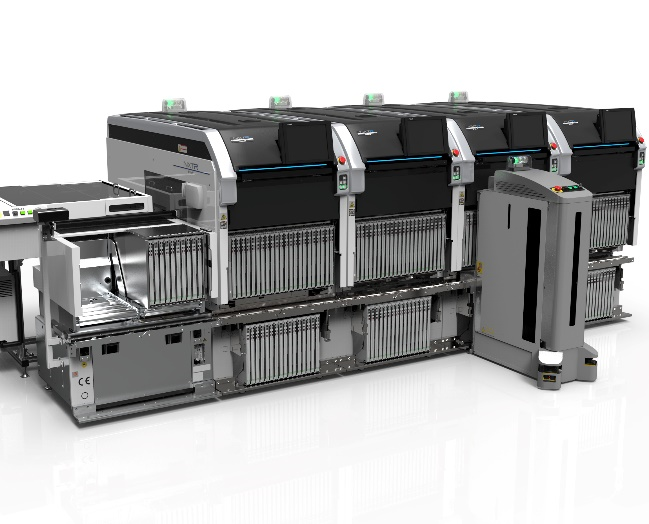
図3 電子部品実装機NXTR
3.2 デジタルツイン技術を活用した提案
3.2.1 モデルの作成とシミュレーション
初めにモデルを作成し(図4)、自動化機器の導入による運用の変更により、ムリ・ムダのない効率的な生産が滞ることなく可能か仮想空間で検証する。シミュレーションはSMTラインの実績データに基づくパラメータによって設定されており、設備・人などの必要資源や生産・段取り替え・部品補給など各作業における負荷率の導出と共に、AGVが何台必要かなど運用に関わる情報も事前に把握できる。
SMTライン全体の動きがシミュレーションにより正確に再現でき、これまで担当者の経験に頼っていた設備選定や運用の決定を仮想空間の中でも客観的な形で見える化することができる。
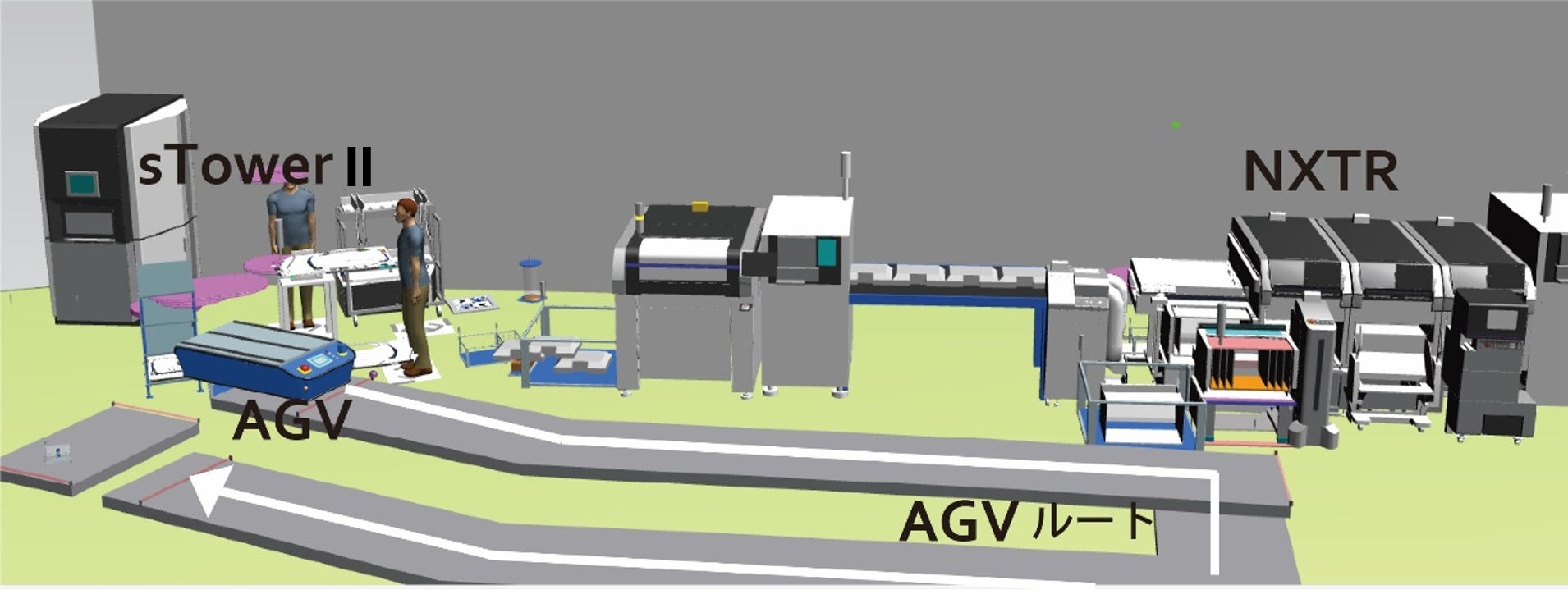
図4 SMTラインを簡略化したモデル
3.2.2 生産を行うためのスケジュール作成
3.2.1の仮想世界で行ったシミュレーションを現実世界の生産へ展開するには正確な生産計画の作成が必要であり、ノウハウとスキルを必要とすることから、これまで専任作業の一つとなっていたのではないだろか。そこで我々は各工程の実績データや実装機を含む各装置のサイクルタイム、生産時間などSMTフロア全体の生産計画を作成するのに必要な各種データを上位システムの生産スケジューラーツールへ提供し、生産計画の具体化を支援している。また、部品切れのタイミング、部品残数、部品のフロアライフ、各ユニットのメンテナンス時期など様々な条件の反映も可能で、SMTフロア全体の正確な生産計画作成作業が少しでも簡単に出来るよう支援している。
3.2.3 オペレーター作業の改善の取り組み
これまで我々は外段取りエリア(次生産に必要な部材の準備を行うエリア)や実装機周りの自動化を積極的に進め、スキルに依存しない高効率な生産の支援に取り組んできたが、現時点でSMTライン全体を完全自動化し、オペレーターをゼロにする所までには至っていない。生産ラインに目を向けると、意図しない突発的なトラブルや作業開始時間・作業の順番によってはダウンタイムが生じることもある。すなわち、これまで述べてきた仮想世界のシミュレーションと現実世界の生産との間にギャップが生じていることを意味し、デジタルツインにより進化するスマートファクトリーを実現しているとは言い難い。ダウンタイム“ゼロ”とする我々の目標は変わらないが、オペレーター作業においてもダウンタイムを限りなく“ゼロ”に近づけるために、時間的な余裕を持って最適な順番で効率的に作業を行えるように作業を案内するソフトウエアを開発している。ピッキング作業(生産に必要な部材を収集する作業)、段取り替え、装置への部材の配膳、部品の補給、メンテナンスなど、ラインサイドで必要な作業がスケジュールの進捗に応じてオペレーターに案内されることで、オペレーターは迷うことなく作業に従事でき、ダウンタイムの最小化に繋がると考えている。引き続き、仮想世界と現実世界のギャップを“ゼロ”にするために、生産状況をリアルタイムに監視・制御し、高品質と高生産性を両立する取り組みを継続し、デジタルツイン技術を活用して進化するスマートファクトリー実現を支援していく。
3.3 SMTラインの自動化による人手作業の革新
SMT工程で作業負荷が高いのは部品に関連する作業であり、部品補給をきっかけに吸着エラーなどいわゆるチョコ停が発生してしまうこともある。これらの課題を解決するために、我々はオートローディングフィーダをはじめ、各種自動化ユニットの開発を行ってきた。この考えを更に発展させ、実装機へフィーダをセットする作業の完全自動化を実現したのが、前述のNXTRである。フィーダの配膳・交換・セットが可能なスマートローダーを世界で初めて実装機へ搭載し、部品交換作業の自動化を実現した。NXTRは装置先頭にあるバッファーステーションにフィーダを配膳するだけで、部品切れや段取り替えなど、スケジュールに応じてスマートローダーが生産デバイスのフィーダと自動で交換していく(図5)。
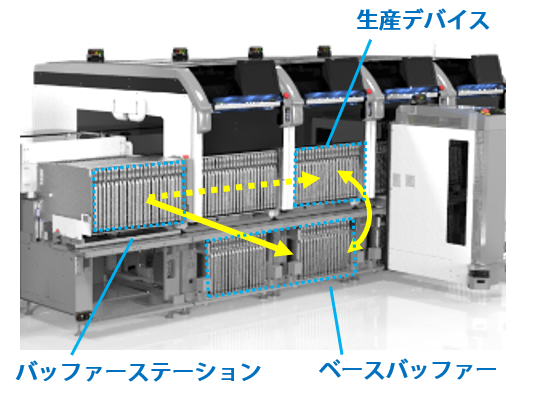
図5 スマートローダーよる部品交換作業
実際にNXTRをSMTラインへ導入し、部品に関連する作業が自動化されると人手作業がどのように変わっていくか、簡単に紹介する。我々は従来の単能工から最終的には多能工のオペレーションへ変革していくことを想定している(図6)。多能工型オペレーションでは、部品に関連する準備や回収作業が1か所で一元化され、最小人数での生産が可能になる。ただし、最少人数での生産対応でオペレーターの負荷率の上昇やダウンタイムが生じては意味をなさない。これらのオペレーションにおいても事前に仮想世界でシミュレーションし、正確な生産計画とオペレーションのナビゲーションツールにより、ムリ・ムダのないオペレーションが実現すると考える。
従来の方法で部品切れや交換のために、フィーダ交換専門の単能工型のオペレーターを多数配置し、対応する。(1ラインを複数人で対応)
スマートローダーを利用することにより、1人がバッファーステーション1か所で部品交換作業することで、多台持ちが可能になる。(1ラインを1人で対応)
バッファーステーションにあるフィーダマガジン(フィーダがセットされているマガジン)をAGVが自動交換することで、オペレーターは装置前の作業が“ゼロ”になる。
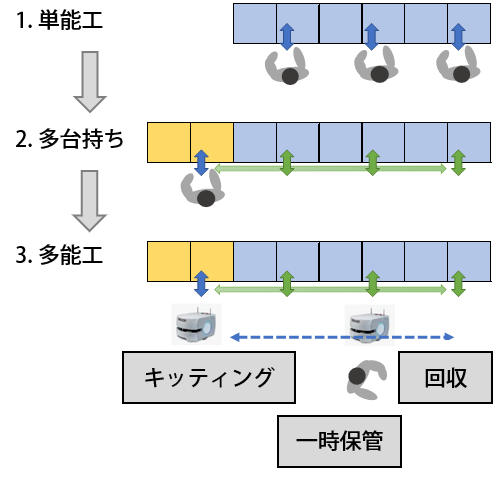
図6 自動化による人手作業の革新
3.4 挿入工程の自動化による人手作業の革新
これまでSMT工程だけでなく、SMT後工程の手挿入工程もモジュール型汎用自動組立機sFAB-Dにより電子部品挿入の自動化に取り組んできた。2021年新たに手挿入工程に対するソリューションとしてsFAB-Dの優れた汎用性・拡張性・生産性はそのままに、一般的な基板組立てに必要な機能に特化したsFAB-SH(図7)と小型多関節ロボットSmartWingのアドバンストロボセルシリーズとして、基板組立ロボセルSW-BA(図8)を開発した。sFAB-SHは、sH08-SHヘッドとsH02-SHヘッドの2種類のヘッドにより、高速挿入から部品高さ55mm・部品重量200gまでの大型部品の挿入までフレキシブルに対応する。また、確実な挿入品質を支援するため、リードチャックやカット&クリンチ機能にも対応している。さらに、はんだ付け後のリペアの原因にもなり得る極性違いによる誤挿入や部品浮きに対して、高精細な画像処理システム、部品を確実に押し込む最適な動作シーケンスと挿入検知動作の組合せにより、不良を未然に防ぐ。一方、SW-BAは水平多関節(スカラ)ロボットにより、コネクタ・コイル・リレー・トランス・大型電解コンデンサなど、限られた部品種での自動化を得意とする。水平多関節(スカラ)ロボットによる部品挿入は新しいロボット技術とは言い難いかもしれないが、SW-BAはSIerによるシステムアップが不要であり、必要機能をパッケージ化し提供することで、低コスト化と短納期化を実現し、手を煩わせることなく即時生産ラインへの投入も可能である。
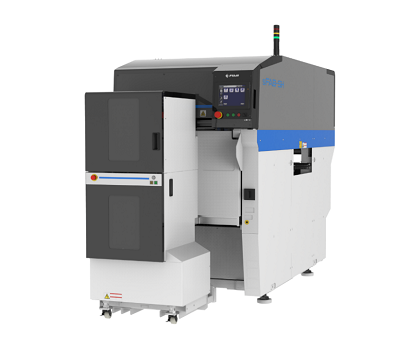
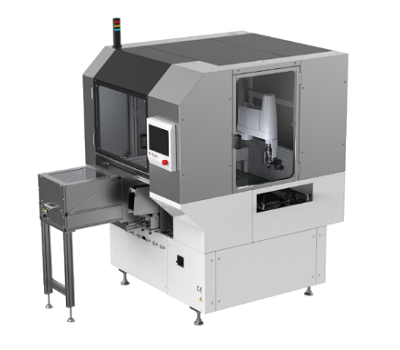
図9に、sFABで小型部品から高さ・重量のある大きい部品まで自動挿入した基板を示す。このように様々な部品の挿入自動化が可能である。挿入の自動化要求は様々であり、部品数点の挿入を低コストで自動化させたいものから、全部品の挿入を高速で自動化させたいなど要求に幅がある。我々は、工程・工場の将来像について顧客の声を正確に捉え、最適なソリューションを提供し、自動化による人手作業を革新させ高稼働・高収益なスマートファクトリー実現に向けた提案を実装機同様に進めていく。
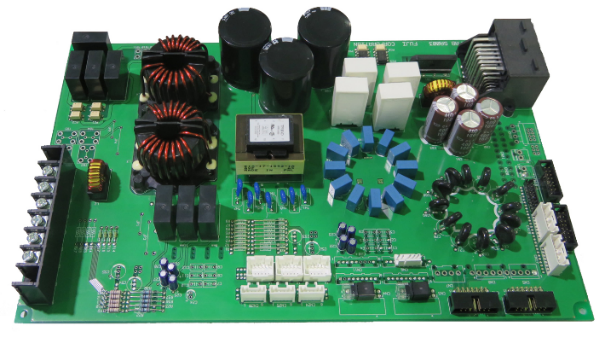
図9 sFABにより自動で挿入された生産基板
4.今後の展望
本稿では、仮想世界のシミュレーションから現実世界のSMT、挿入工程までの我々の取組みを紹介した。今後もSMTラインのデジタル連携により、デジタルツインで進化するスマートファクトリーの実現を顧客目線で支援する。我々自身、仮想世界と現実世界のギャップを“ゼロ”にするための手段の一つが自動化であり、決してそれだけが答えではないと考えている。顧客が真に何を望んでいるかを捉え、顧客の期待を上回り、感動いただけるような製品、サービスの企画を今後も行っていく所存である。